
Later, it was applied to a number of functional ceramics in a number of ways including LaGaO 3 ( Zha et al., 2001), ZnO ( Bell et al., 2004), and Sr 0.5Ba 0.5Nb 2O 6 ( Chen et al., 2006), etc. Since its invention in 1991 gelcasting has been widely used for the fabrication of structural ceramics, including Al 2O 3 ( Young et al., 1991), SiC ( Zhou et al., 2000), and Si 3N 4 ( Huang et al., 2000), etc. Furthermore, gelcasting may be developed to fabricate complex-shaped ( Cai et al., 2003) or fine-structured ( Guo et al., 2003) ceramic parts that are rather difficult or even impossible to be formed by the conventional dry pressing method. In contrast, such a ceramic disc can be easily made by gelcasting via a simple ring-shaped mold at much less cost. For example, to make a ceramic disc with a diameter of 20 cm by dry pressing, a load of hundreds of tons is required.
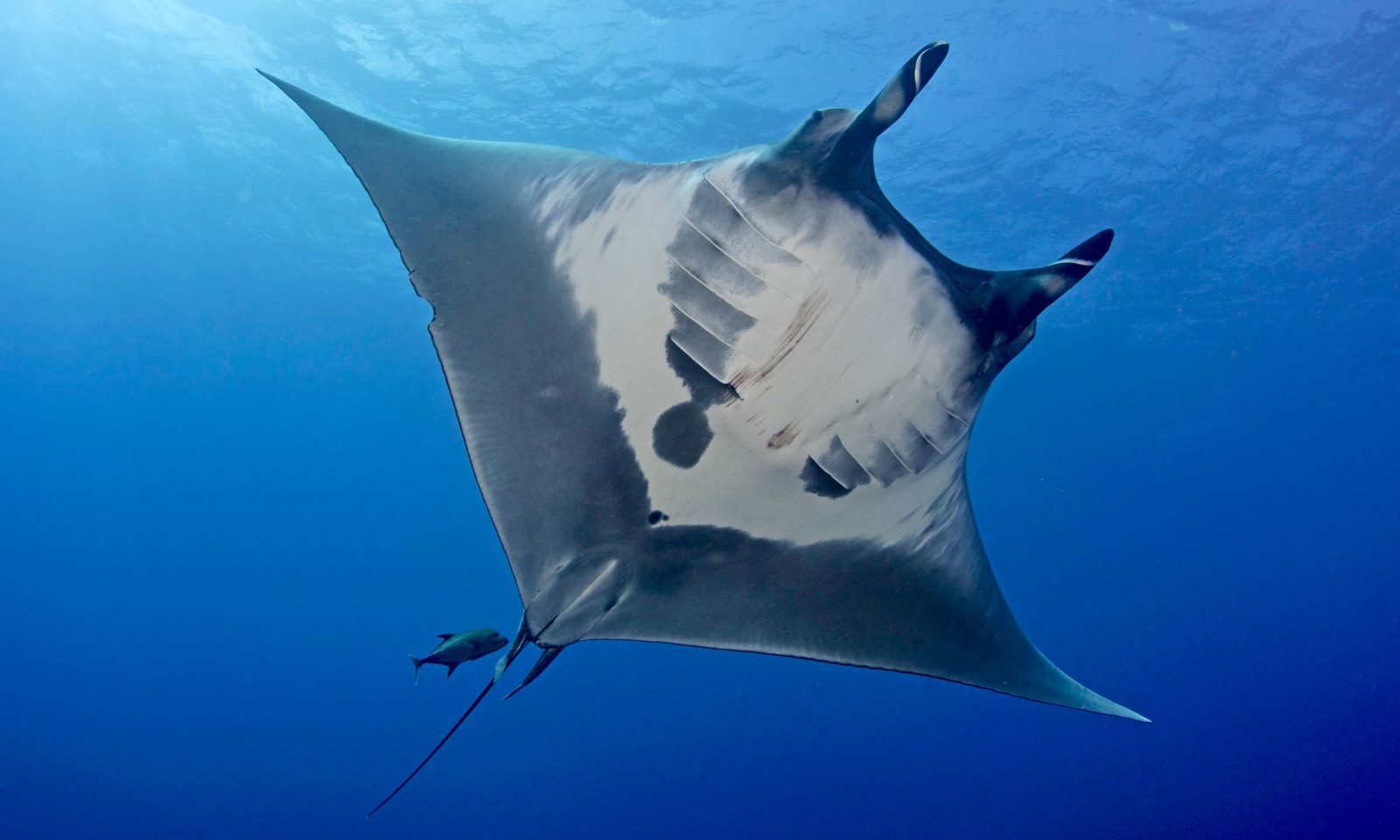
#MINITUBE MANTA FREE#
As a pressure free method, it can also be used in fabricating large ceramic components that have simple shapes. Gelcasting may be seen as a milestone in fabricating complex-shaped ceramic parts since it has initiated a new branch of research in ceramic processing due to its intriguing properties of near-net-shape forming, high green strength, and low binder concentration, etc. When heated, the monomer and cross-linker polymerize to form a three-dimensional network structure, thus the slurry is solidified in situ and green bodies of the desired shape are obtained, which consists mainly of ceramic powders with a low polymer content. In the technique, a high solids loading slurry obtained by dispersing the ceramic powders in the pre-mixed solution containing monomer and cross-linker is cast in a mold of the desired shape. Among the many wet forming techniques, aqueous gelcasting represents the latest improvements. Since in these techniques the ceramic powders are dispersed in a liquid medium and thoroughly mixed, wet forming techniques have the advantages of reducing some structure defects that are difficult to remove in dry pressed ceramic parts. To resolve the problems associated with the conventional dry pressing, new wet forming techniques, such as gelcasting ( Omatete et al., 1991), electrophoretic casting ( Biesheuvel et al., 1999), hydrolysis assisted solidification ( Novak et al., 2002), and direct coagulation casting ( Graule et al., 1996), etc., are becoming increasingly attractive for advanced ceramic materials. One of the most serious disadvantages of dry pressing lies in the difficulty in fabricating high quality large and complex-shaped ceramics or ceramics with a fine structure, which are required for various devices.

If the ceramic parts are unable to have pressure transmit suitably for a uniform pressed density then isostatic pressing may be used. Therefore, large ceramic parts require a much higher compacting force. The pressure is around several tens of MPa or higher. In this technique, dry powders containing organic binder are filled into a solid mold, then dry ceramic green bodies with the shape of the mold cavity are formed under mechanical or hydraulic compacting presses selected for the necessary force and powder fill depth. Dry pressing is the most commonly used ceramic forming technique. A certain shape formation technique is required to make ceramics with the desired shapes.
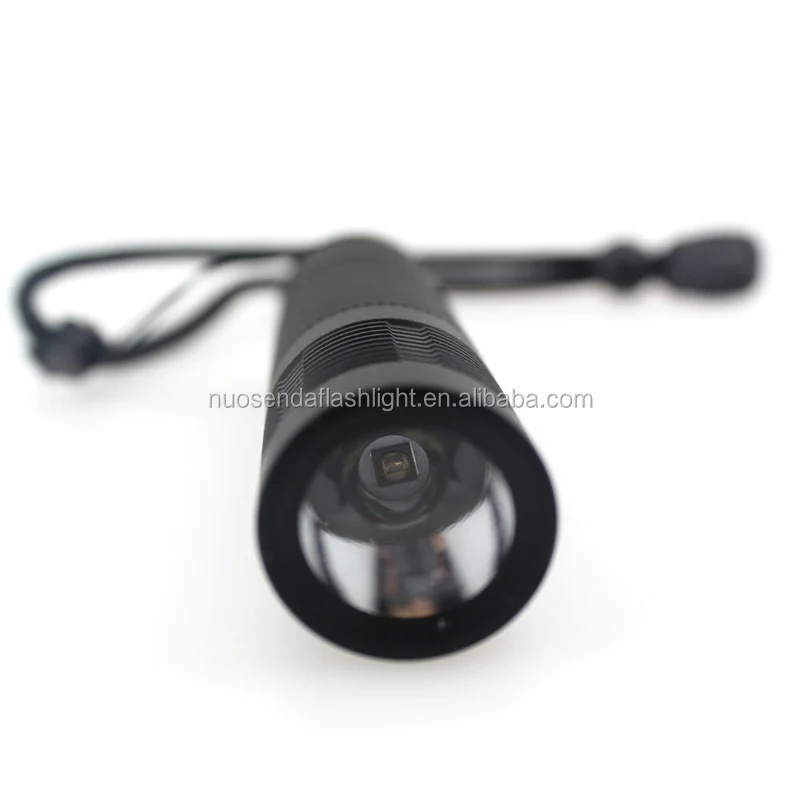
Ferroelectric ceramics may be seen as the most important type of ferroelectric materials, which have been used in a wide spectrum of electrical and microelectronic devices, including underwater transducers, micro-pumps and valves, ultrasonic motors, thermal sensors, probes for medical imaging and non-destructive testing, and accelerometers, etc ( Cross LE, 1996 Setter et al., 2000).įerroelectric ceramics used in the devices have various shapes.
